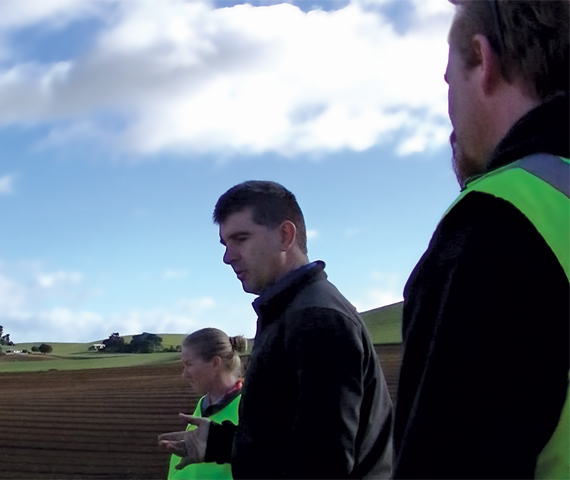
Onion crop profile & processing cost reduction
Project Objectives
- Analyse the characteristics sought by Harvest Moon’s onion customer base
- Produce a target crop profile
- Examine the value chain of the onion production system and identify ways to improve its efficiency and effectiveness
- Install new packaging equipment and reconfigure the processing, grading and packing line in order to improve the efficiency and effectiveness of the line
Project Team
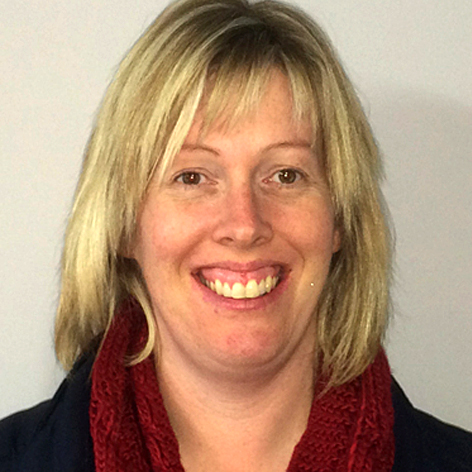
Lisa Hatten
Harvest Moon
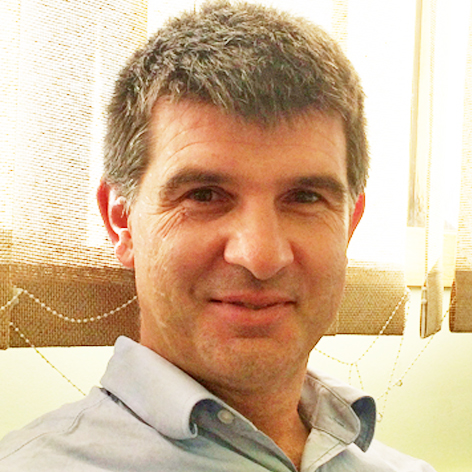
Andrew Doran
Harvest Moon
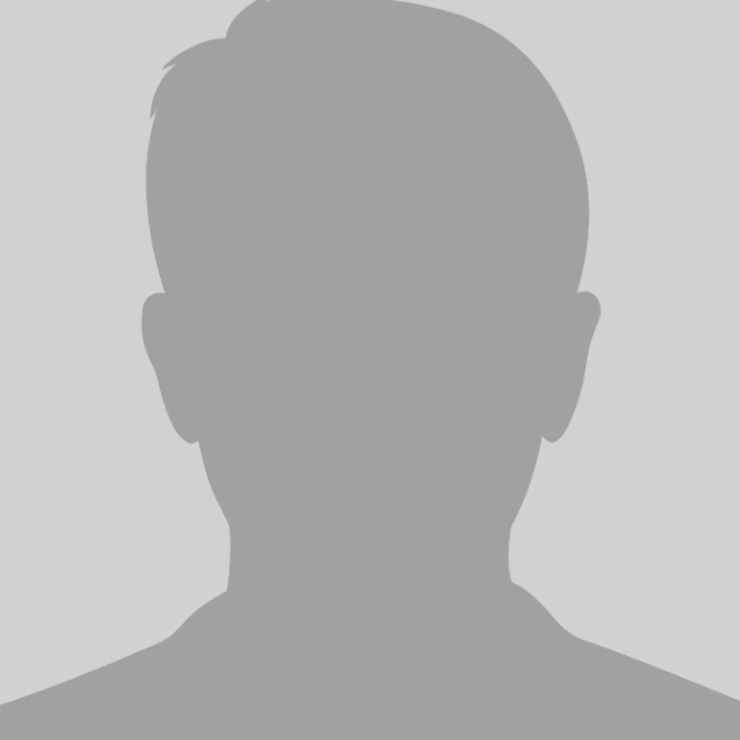
Ben Shankland
Harvest Moon
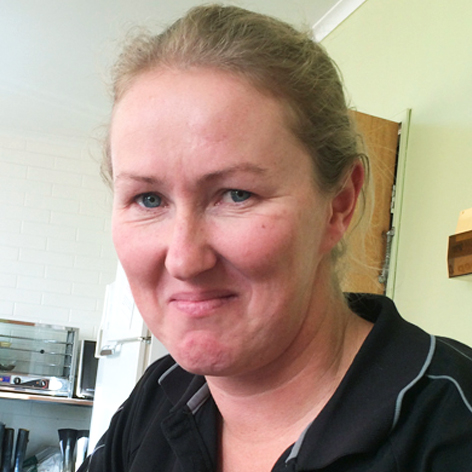
Elesha Spillane
Petuna
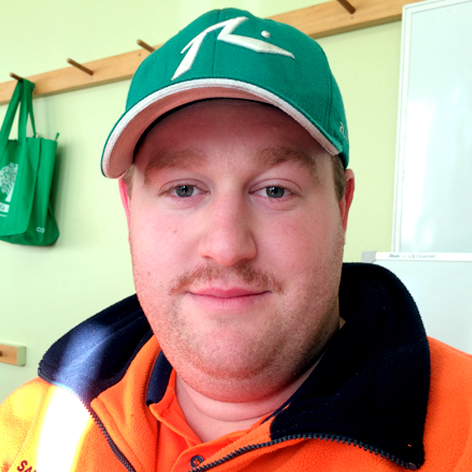
Matthew Saunders
Direct Edge Manufacturing
Facilitator
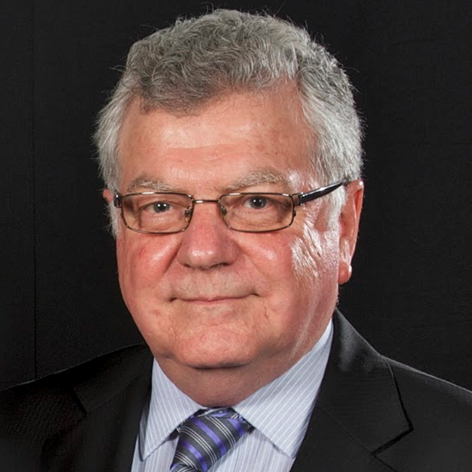
Bob Cother
The Action Learning Institute
Key measurables
- Alignment of crop produced with customer requirements
- Efficiency and effectiveness of receival, processing, grading and packing of onions
- Improved profitability of Harvest Moon’s onion enterprise
Companies involved
- Harvest Moon
- Petuna
- Direct Edge Manuafacturing
Approach taken
- Detailed briefing from senior management
- Field visit, initial tour of onion processing operations and storyboard of initial impressions
- Process Mapping
- Stakeholder interviews
- Cause and Effect Analysis on cost per tonne for packaging
- Direct observation of production and processing
- Video studies and analysis
- Data collection and analysis
- Identification and evaluation of options
- Specification of seven projects for implementation stage:
- Crop Profile Strategy
- Crop Sampling
- Onion Line Operation
- Prepack Location
- Packing Cell Design
- Grading and Waste
- Cool Store Energy Use
Summary of outcomes
- Less hectares required to achieve customer requirements
- Improved line balancing with more effective allocation of crops to customers
- Reduced cost per tonne through improved utilisation of personnel
- Reduced cost, faster response time, less Work-in-Process
- 15-20% improvement in labour productivity
- Improved profitability by minimising unnecessary downgrading of product
- Reduced energy usage and product degradation in cool stores