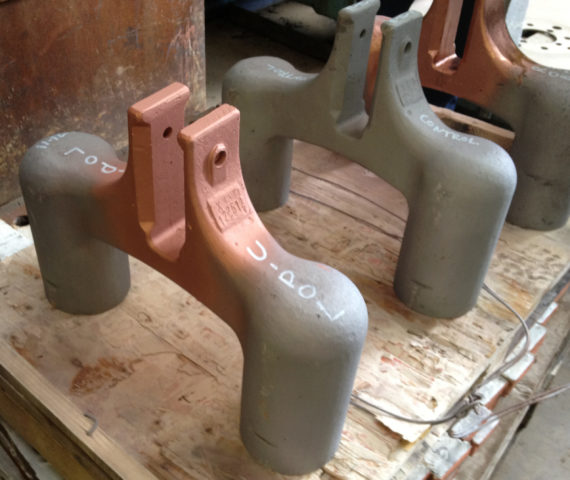
Anode rod repair
Project Objectives
- Analyse the current process for anode rod repair including transport to and from CPT engineering
- Recommend and justify improvements to the process to reduce cost
Project Team
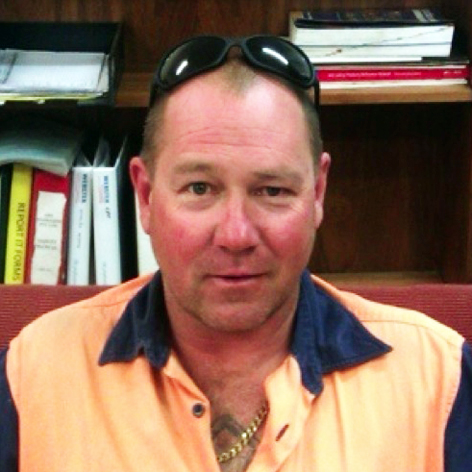
Leigh Edgerton
CPT Engineering
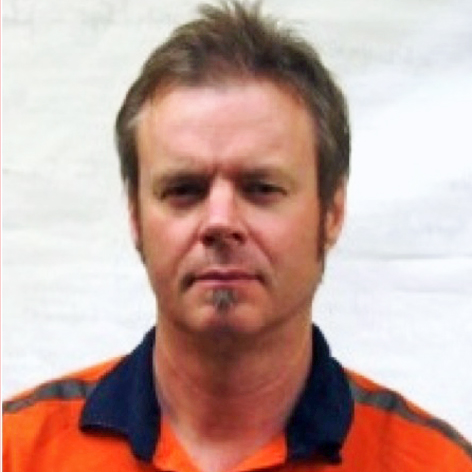
Ian Hutchison
Bell Bay Aluminium
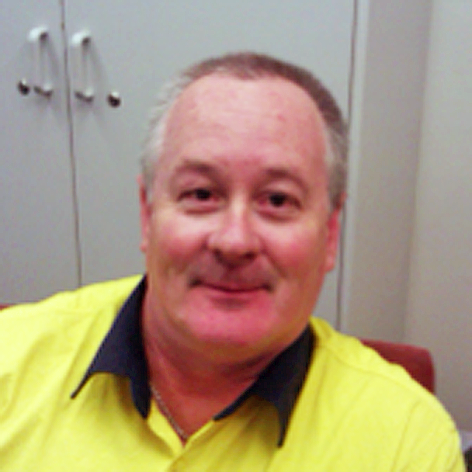
Duane Bird
Tas-Fab Laser Services
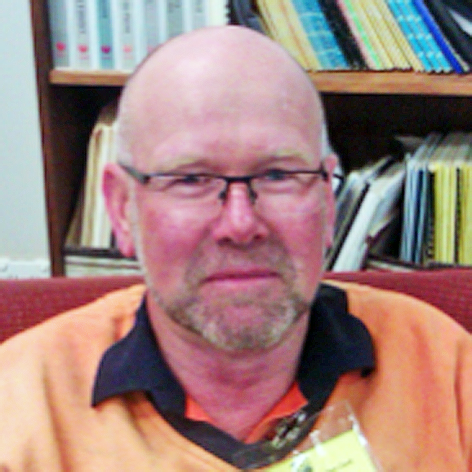
Ian Harris
ACL Bearing Co.
Facilitators
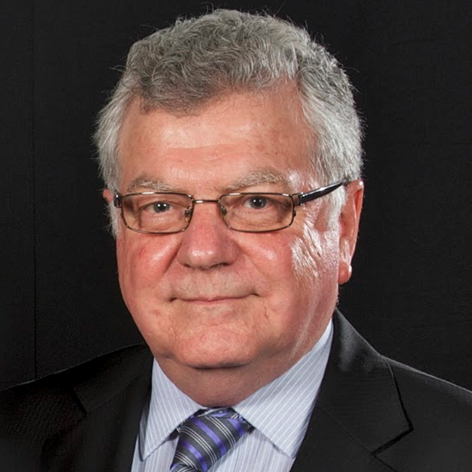
Bob Cother
The Action Learning Institute
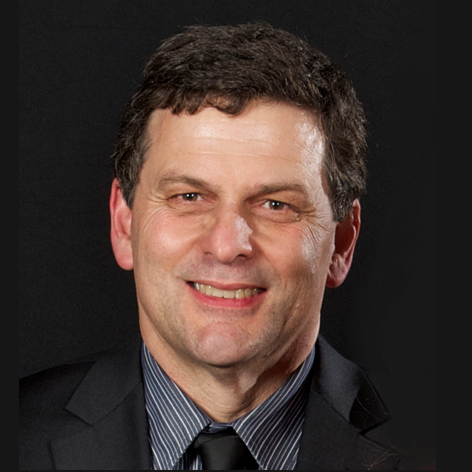
Bill Woodworth
Bell Bay Aluminium
Key measurables
-
Annual cost of refurbishing anode rods
Companies involved
-
CPT Engineering (co-host)
-
Bell Bay Aluminium (co-host)
-
Tas-Fab Laser Services
- ACL Bearing Co.
Approach taken
- Site tour and observation of production processes
- Storyboarding of first impressions of current process
- Stakeholder consultation
- Spaghetti Diagram of current layout and exploration of layout options
- Cost breakdown of repair process and effects of longer weld life
- Reviewed cracked weld reject criteria and compared reject rates across shift teams at Bell Bay Aluminium
- Established implementation plan to:
- Eliminate rejection of rods still within acceptable standard
- Extend the life of the weld by 10-20% through application of weldable primer at source and custom design ‘rod dressing’ station
- Eliminate hazardous substance (Rustillo) used to prepare weld area
Summary of outcomes
- Estimated annual savings of over $100,000 through longer rod assembly life
- 25% reduction in reject rate, delivering a further $60,000 annual saving
- Hazardous substance eliminated from process
- Multi-million dollar contract awarded to CPT Engineering by Bell Bay Aluminium to replace entire fleet of 13,000 anode rods over four years