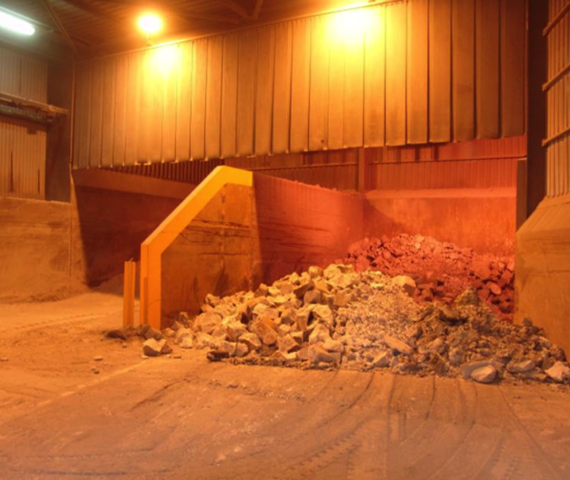
Bath plant material flow
Project Objectives
- Review the fines material flow of the inputs and outputs to the bath plant
- Establish and implement a system to ensure efficient movement of material to and from the bath plant, considering input material fluctuations
Project Team
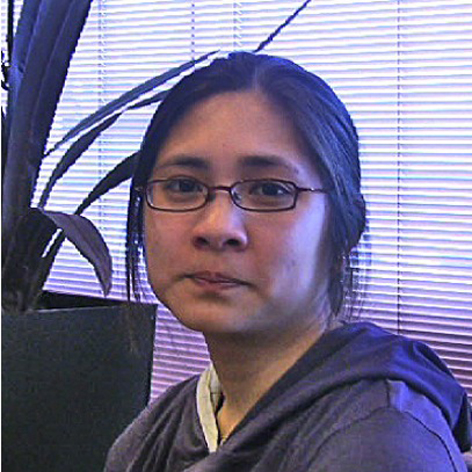
Jessica Rouse
Bell Bay Aluminium
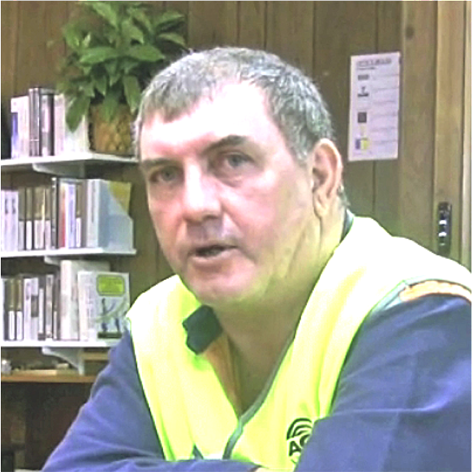
John Collins
Bell Bay Aluminium
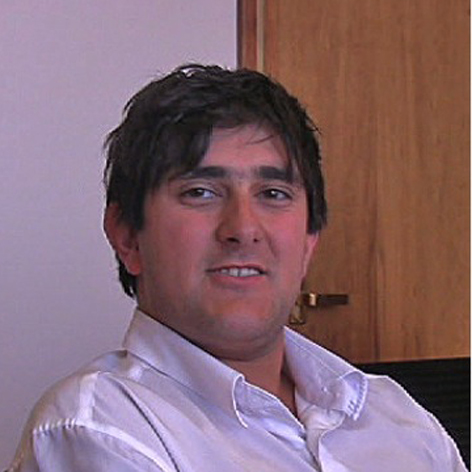
Manuel Matteo
Tamar Valley Dairy
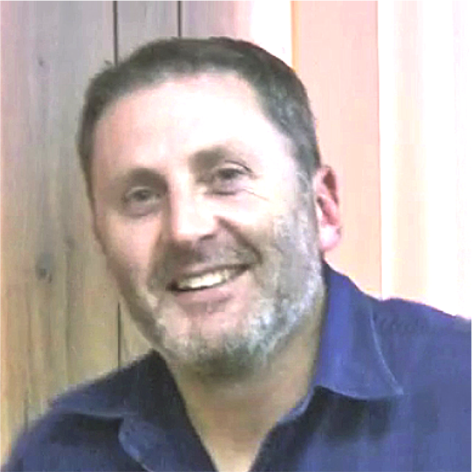
Paul Grant
ACL Bearing Co.
Facilitator
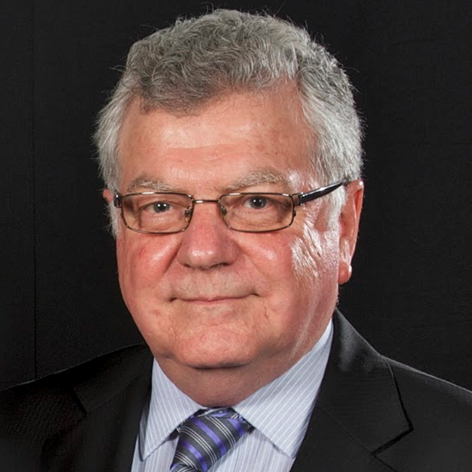
Bob Cother
The Action Learning Institute
Key measurables
- Fines/Coarse target ratio 1:1 to 1.4:1
- C5 conveyor ‘bog downs’ less than 10 per month
Companies involved
- Bell Bay Aluminium (host)
- Tamar Valley Dairy
- ACL Bearing Co.
Approach taken
- DMAIC approach applied
- Site tour and observation of process
- Storyboarding to reflect on current process
- Reviewed available data to further define the problem
- Collected relevant data to identify inconsistencies in Fines/Coarse ratio across shift teams
- Interviewed key stakeholders
- Root cause analysis
- 5 Whys
- Cause and Effect Diagram
- Identification of root cause as ‘divergance in silo levels’
- Brainstorming to develop ideas to address the root cause
- Refined improvement ideas and developed implementation plan
- Established controls to sustain the improvement, eg. employee training and ‘full’ limit markings on bunkers
Summary of outcomes
- Comparisons of before/after I-MR Charts of Fines to Coarse Ratio by each crew show that the process is now within the target ratio
- Reduced alumina content has enabled a higher proportion of fines in the bath cover, significantly reducing the stockpile of legacy fines material and freeing up storage space for other uses