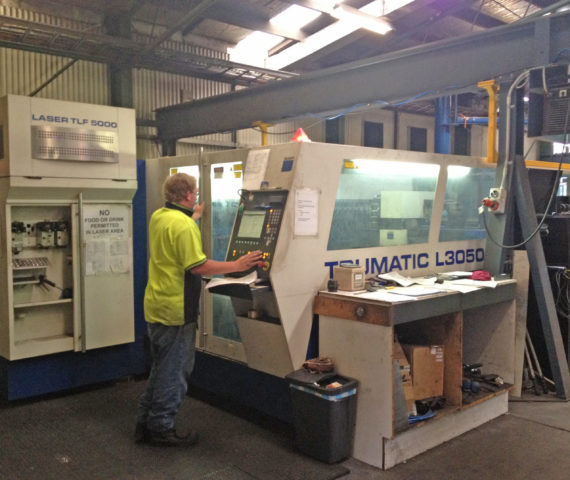
Shop floor information
Project Objectives
- Establish a framework for:
- Job definition and skills required for the job
- Processes and documentation
- Visual management and visual communication in the workplace
- Integration with the TKO system
Project Team
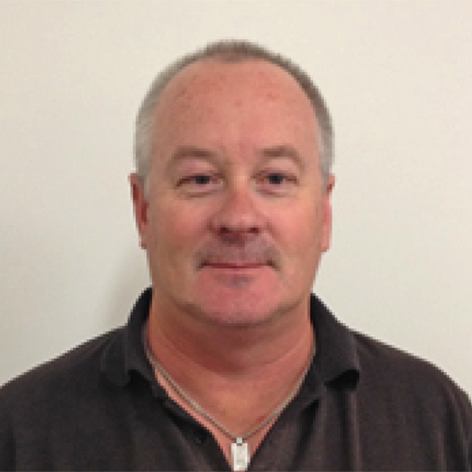
Duane Bird
Tas-Fab Laser Services
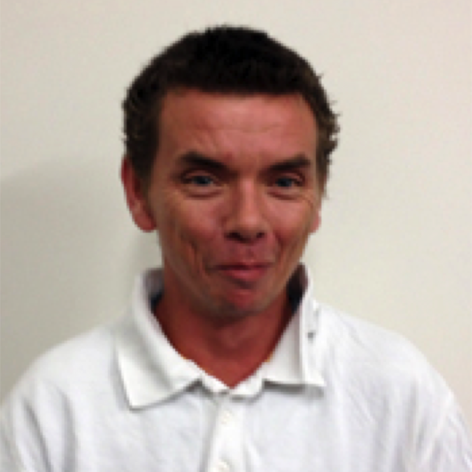
David Thomas
Tas-Fab Laser Services
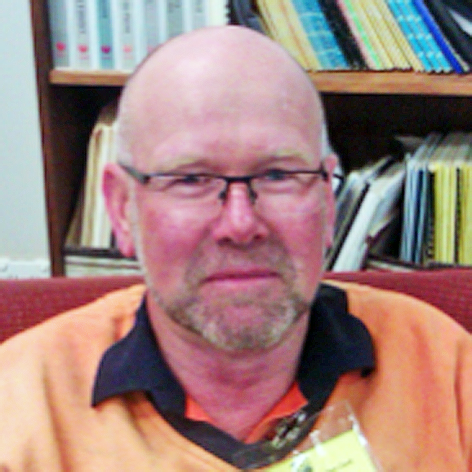
Ian Harris
ACL Bearing Co.
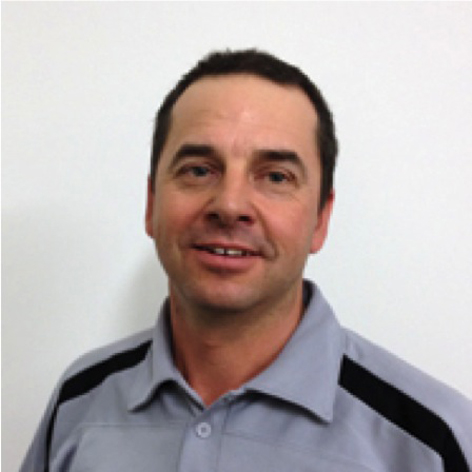
Brian Lockhart
Bell Bay Aluminium
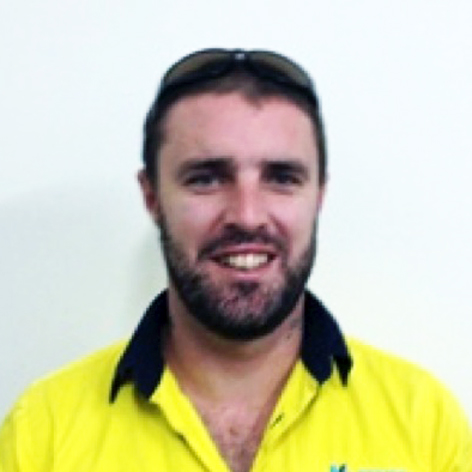
Nick Williams
Kempe Engineering
Facilitators
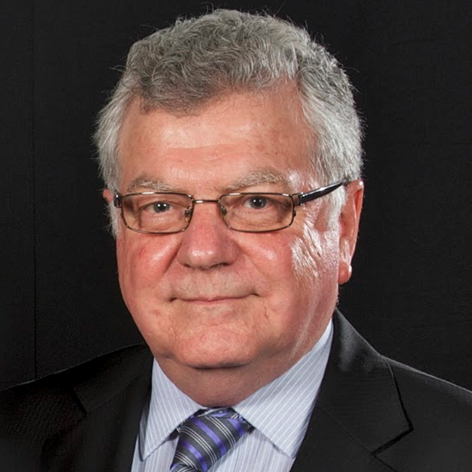
Bob Cother
The Action Learning Institute
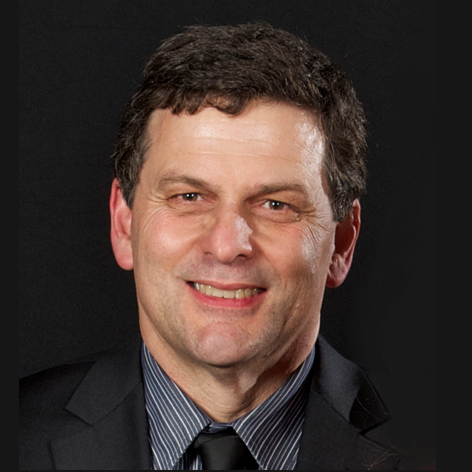
Bill Woodworth
Bell Bay Aluminium
Key measurables
- Within five weeks, to have developed the framework, using the laser operator job role as the prototype
- Within six months, to have rolled the framework out across the Profile Cutting Department
Companies involved
-
Tas-Fab Laser Services (host)
-
Bell Bay Aluminium
-
Kempe Engineering
- ACL Bearing Co.
Approach taken
- Value Stream Mapping of laser services
- Collection of key data for Laser 3050
- Employee interviews
- Legislative review
- Developed task list for operator to determine information required
- Explored hard copy and display options
- Trialled (existing) online TKO system
- Developed a Profile Cutting Department Menu on existing workstation terminal:
- Standard Operating Procedures
- Troubleshooting
- Risk Assessment
- Skills Matrix
- Job Descriptions
- Training Plan
- Developed procedure for assessing skills and training new recruits
- Identified options for external training and relevant funding sources
Summary of outcomes
- Accelerated development of employees
- For employees, greater job satisfaction and a pathway to achieve their potential
- Freed up supervisor to concentrate on supervision and team development for:
- smoother more consistent work
- flow
- less rework
- shorter lead times
- higher quality output