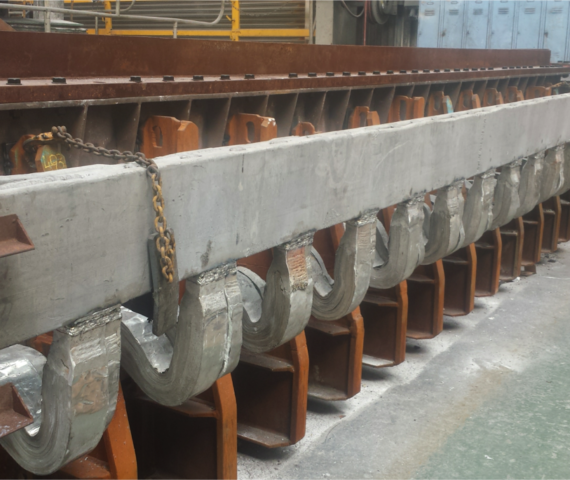
Cathode tail manufacture
Project Objectives
-
Develop and implement a sustainable and cost effective manufacturing process for the manufacture of 9B type reduction cell collector bar tails for Bell Bay Aluminium
-
Identify possible methods for converting old tails to new design tails
-
Also develop a cost effective recycling process for used 9B collector bar tails
Project Team
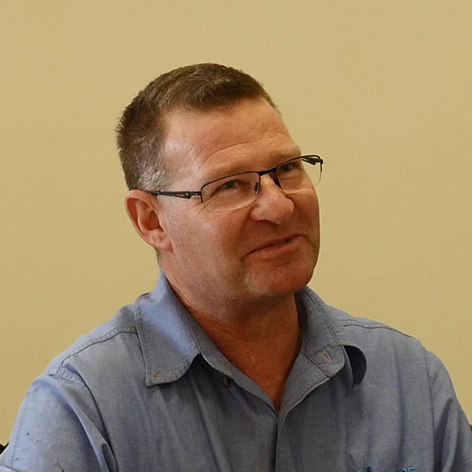
Tom Frain
Kempe Engineering
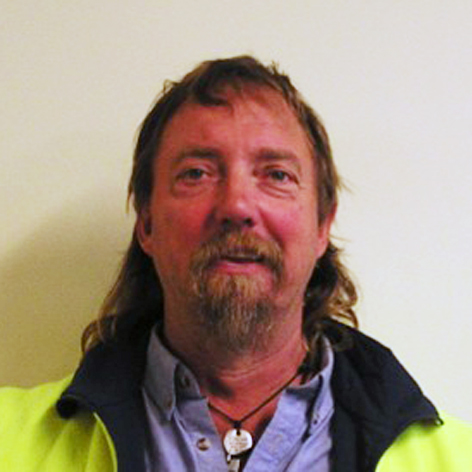
Roger Aalbregt
Kempe Engineering
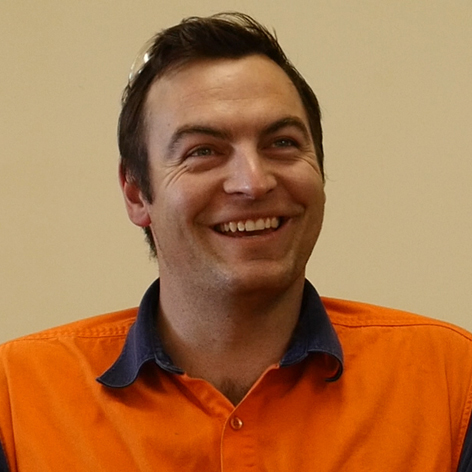
Brendan Sherriff
Bell Bay Aluminium
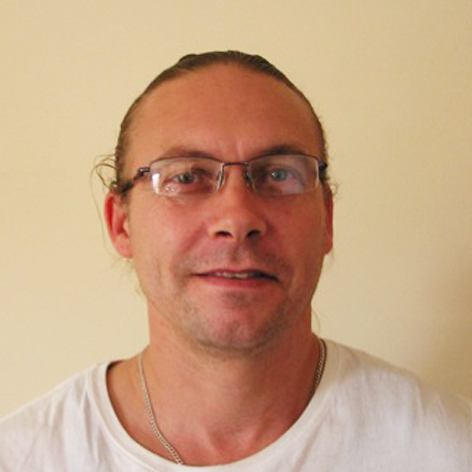
Peter Wilkins
Tasmanian Alkaloids
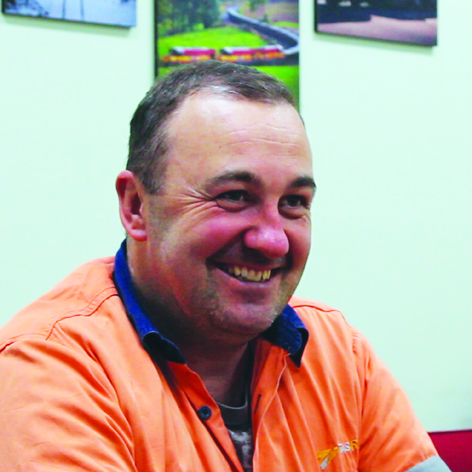
Trent Swain
TasRail
Facilitators
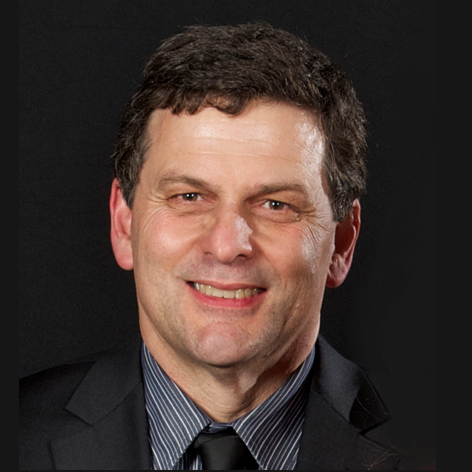
Bill Woodworth
Bell Bay Aluminium
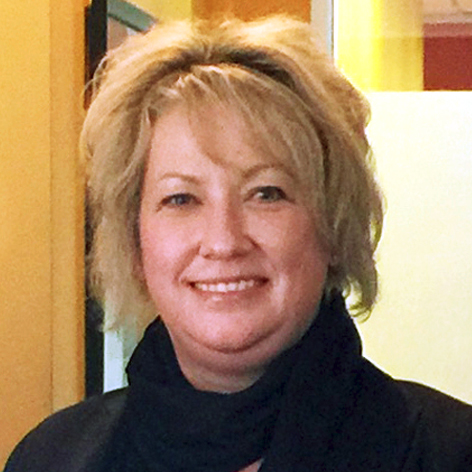
Roxanne Chugg
Excellent Outcomes
Key measurables
-
Product cost competitive with overseas supplier
-
A product that is equal or superior in performance than imported equivalent
Companies involved
-
Kempe Engineering (co-host)
-
Bell Bay Aluminium (co-host)
-
TasRail
-
Tasmanian Alkaloids
Approach taken
- Produced a detailed costing model to establish if new design was viable
- Highlighted areas for improvement in costing model
- Visited BBA to hear voice of customer
- Developed a functional and efficient manufacturing cell design
- Created future state value stream map
- Developed controls for managing new process
- Used computer modeling to prove effectiveness of tail design
- Designed implementation plan
- Value stream mapping
- Tools used:
- WORMPIT (waste walk)
- Time in Motion Study
- Spaghetti diagram
- Focus groups
- Trystorming
- Financial modeling
Summary of outcomes
-
Cost targets met through efficiencies in manufacturing cell
-
Ongoing mV savings per annum of approx. $40,000.00+ per year even after the implementation of the project
-
Maintaining the personnel and skill base in the local area
-
Investment in the local economy
-
Better spread of any capital investment
-
Better weld characteristics and weld times in reconstruction
-
Better control over the supply process and not having to hold inventory
-
Reduced CO2 emissions due to recycling