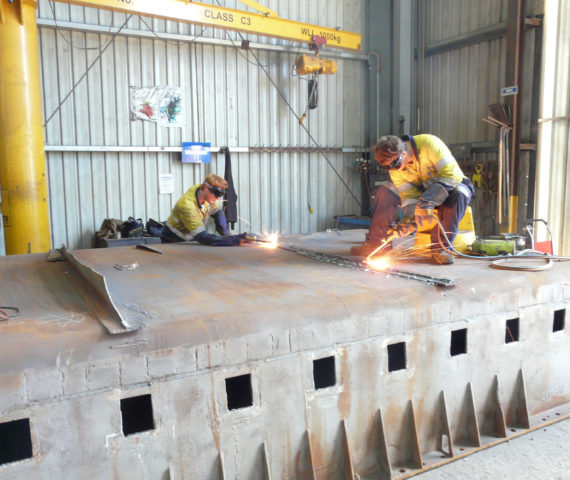
Pot shell refurbishment
Project Objectives
- Analyse the current process for pot shell refurbishment and transport to and from Kempe engineering
- Recommend and justify improvements, that will reduce the cost of the process by 15% per annum
Project Team
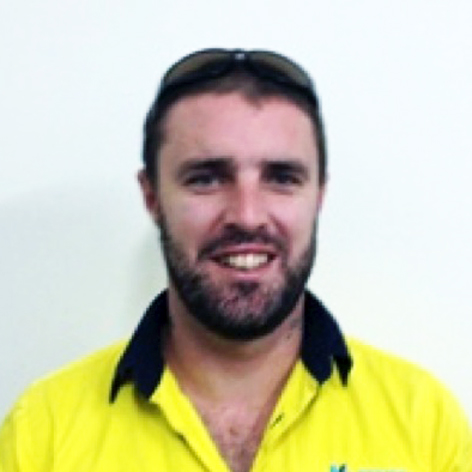
Nick Williams
Kempe Engineering
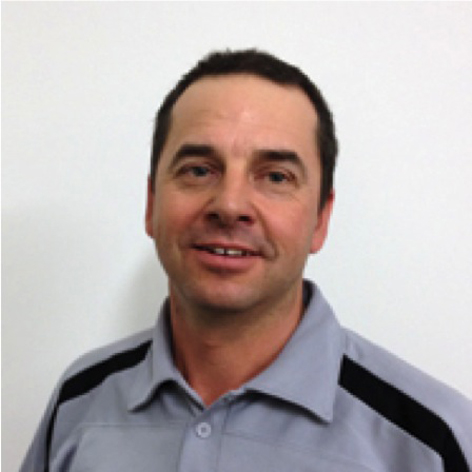
Brian Lockhart
Bell Bay Aluminium
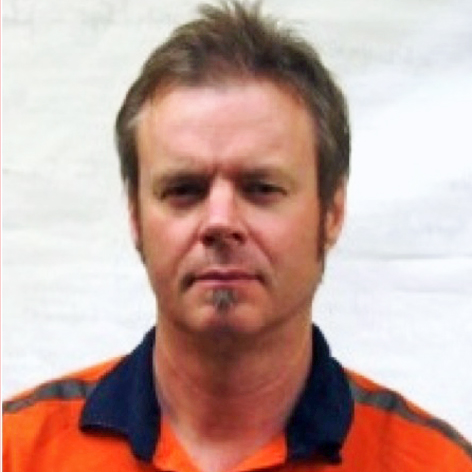
Ian Hutchison
Bell Bay Aluminium
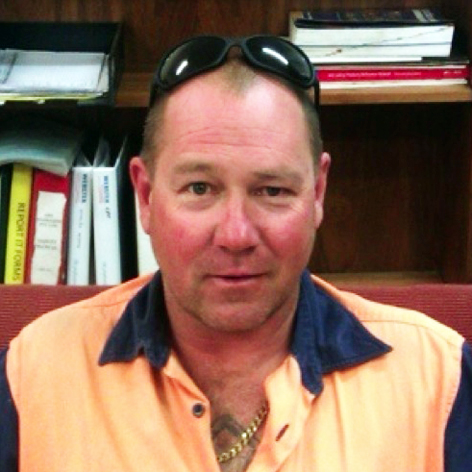
Leigh Edgerton
CPT Engineering
Facilitators
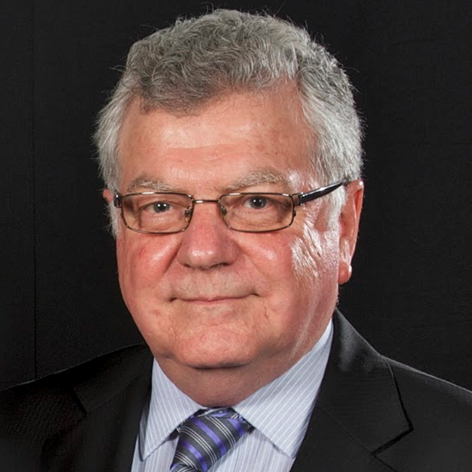
Bob Cother
The Action Learning Institute
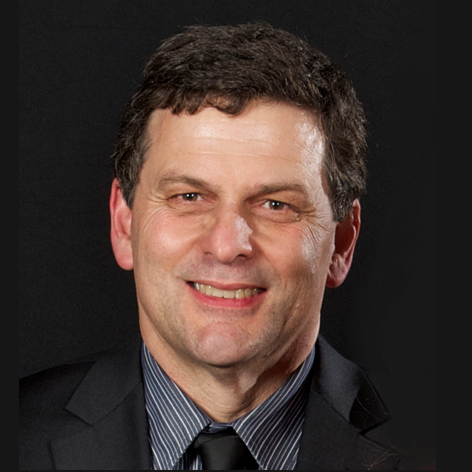
Bill Woodworth
Bell Bay Aluminium
Key measurables
-
Overall cost reduction of 15% per annum
- Target average labour hours per shell
Companies involved
-
Kempe Engineering (co-host)
-
Bell Bay Aluminium (co-host)
-
CPT Engineering
Approach taken
- Site tours and observation of processes at Kempe and BBA
- Value Stream Mapping of current processes
- Brainstorming sessions to generate improvement ideas
- Interviews with relevant stakeholders at both sites
- Root cause analysis and Cause/Effect analysis
- Development of improvement options, including:
- Improvements to the delining process at Bell Bay, which was causing significant damage and affecting work flow at Kempe Engineering
- Manufacturing cell design at Kempe including customised equipment
- Presentation of recommendations to senior management, including cost/benefit analysis
- Preparation of implementation plan
Summary of outcomes
- Cost and labour hour targets met through improved workflow at Kempe
- Significant additional savings through recycling of the ‘tails’ that conduct electricity into the pot shell
- Business retained by Kempe that had been lost or could be lost to offshore suppliers