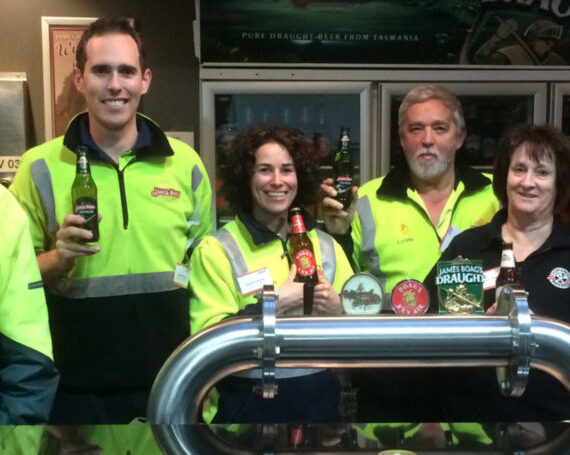
Line Changeover
Project Objectives
-
Minimise the time that neither line is producing and maximise the time that one or the other line is producing
-
Visual management of filler stopping on one line to filler starting on the other line
-
Minimise the time the line gets to rated speed
Project Team
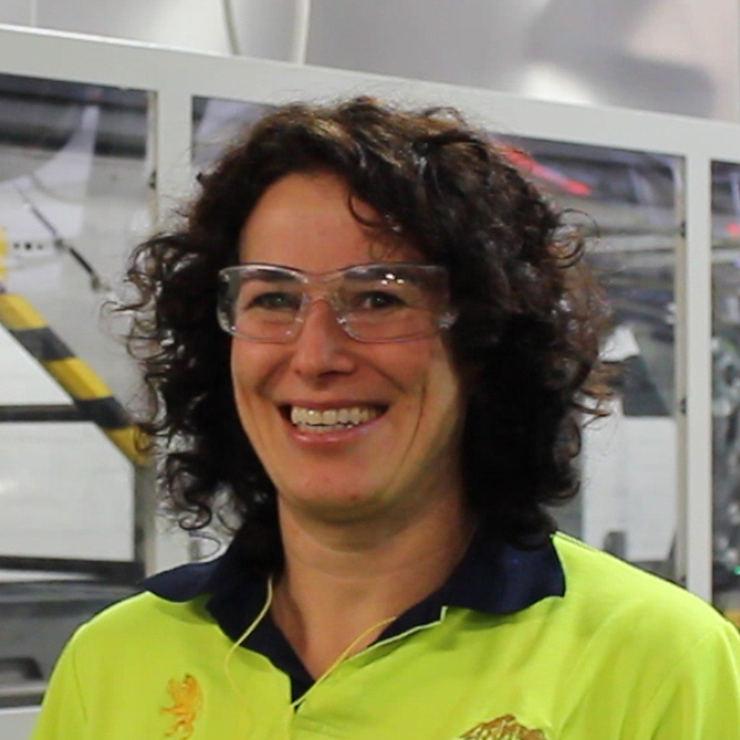
Alex Warren
J Boag & Son
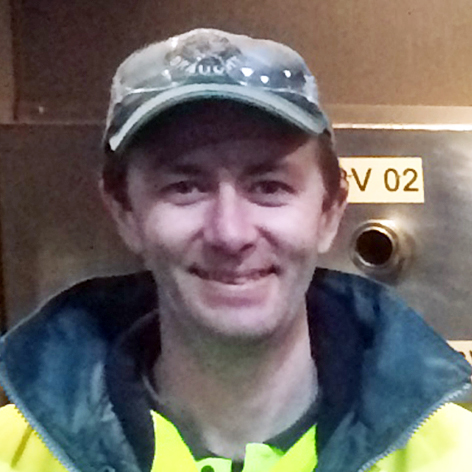
Monty Clark
J Boag & Son
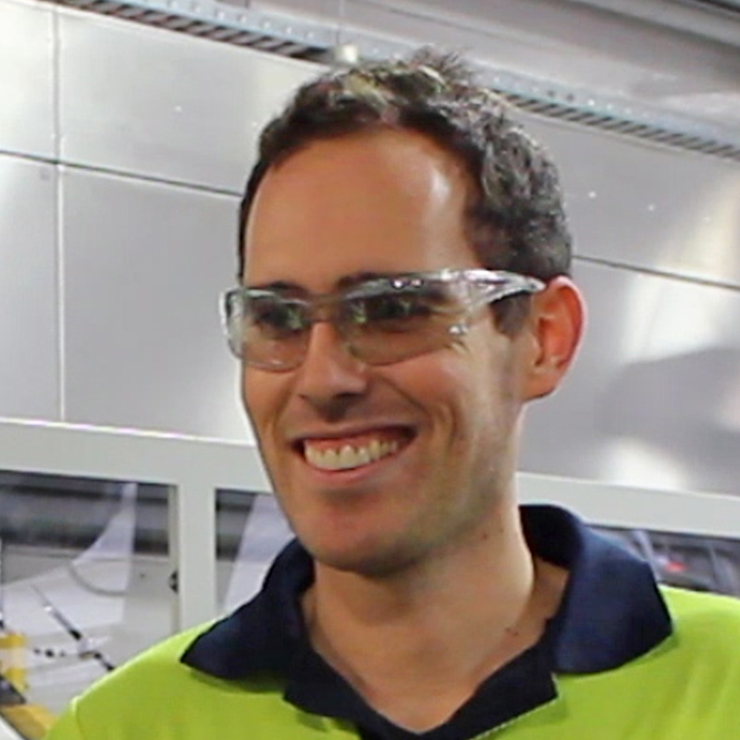
Chris Whitfield
J Boag & Son
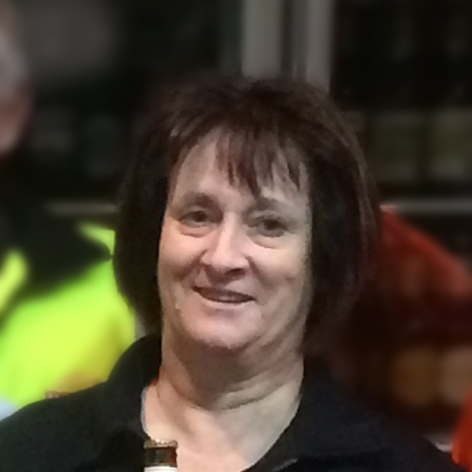
Diane Roberts
Tasmanian Bakeries
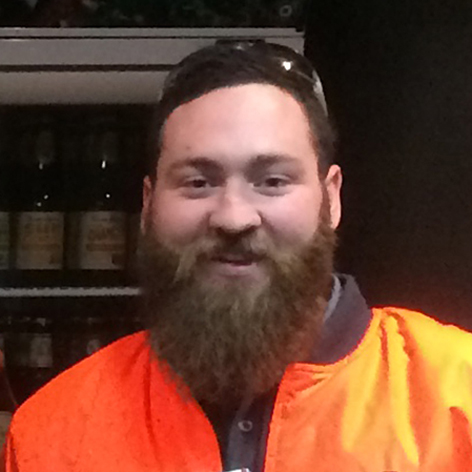
Rayne McCreadie
Direct Edge Manufacturing
Facilitators
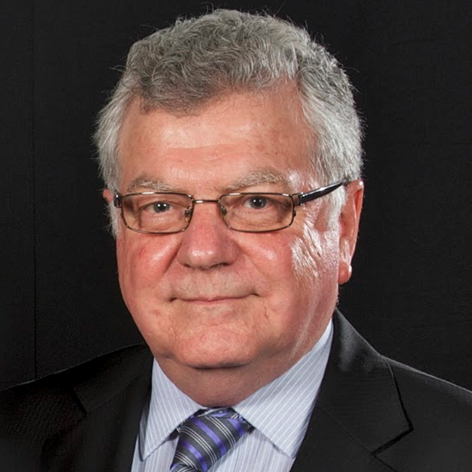
Bob Cother
The Action Learning Institute
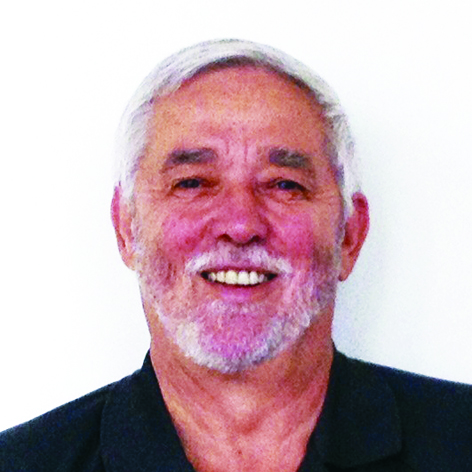
Les Souster
Just Lean Associates
Key measurables
-
Overall Equipment Effectiveness of Line 1 & 2
Companies involved
-
James Boag & Son Brewery (host)
-
Tasmanian Bakeries
-
Direct Edge Manufacturing
Approach taken
-
Defined current process state
-
Expectation of project, line capabilities, OEE target, impact on customers presented by senior managment
-
Team toured operation (Line Separation caused complexities and communication barriers)
-
Current Line 1 and 2 processes mapped
-
Story board of initial impressions
-
Stakeholder interviews
-
Data collected and analysed to find ‘black hole’ in changeover time
-
DMAIC and Cause/Effect used to determine root cause
-
Key issues identified and action plans addressing each issue created
-
Gantt chart used to plan implementation
-
Regular meetings with Project Champion to monitor progress
Summary of outcomes
-
Line change over average time reduced from 4 hours to 2 hours
-
Better planning resulted in changeover consistency
-
Ten hours of extra production time in the week
-
Better standard work task completion on changeover – now tracked at Tier 1 level
-
OEE improved by approx. 20% and sustained over next three months, currently running just under 80%
-
Plan is now to set a two hour window for changeover