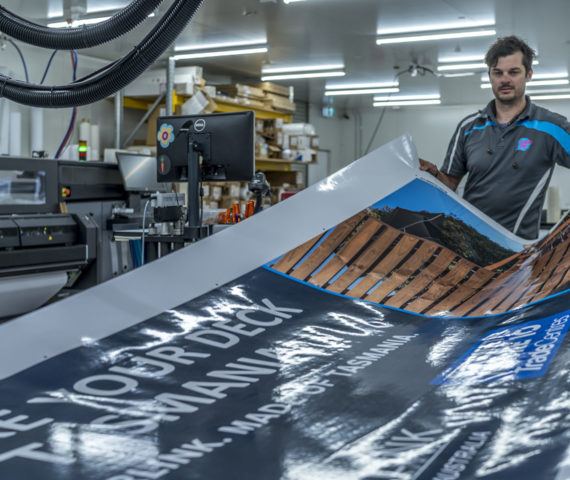
Elimination of waste in process
ThinkBig Printing is actively recycling almost half of its production wastes, including aluminium, corflute and cardboard. Remaining wastes are predominantly vinyl; options for recycling vinyl are very limited and not available in Tasmania. The business is seeking to reduce vinyl waste to landfill by eliminating errors in production that cause avoidable waste.
The Project
Reduce wasted materials and labour by improving the accuracy of reporting of product non-conformance and eliminating extra work required to correct nonconformities (rework).
Identify root causes, improve management systems already in place, and involve employees in seeking solutions to prevent recurrence.
Objectives
- Improve accuracy of non-conformance reporting.
- Reduce rework across the production process and waste to landfill.
Targets
- 100% recording of nonconformance.
- 50% reduction in rework.
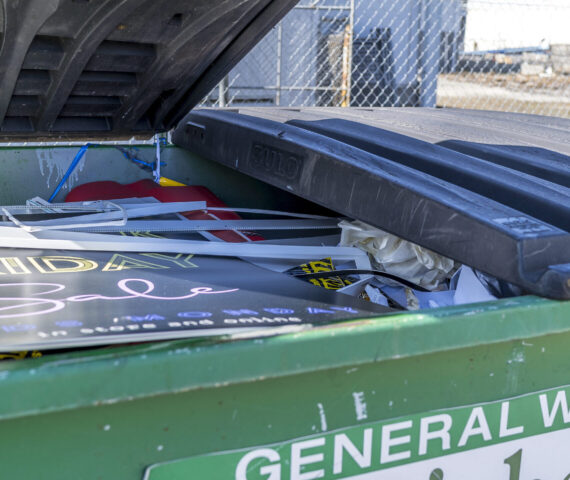
Most of the waste generated in production originates from offcuts. The second largest waste is defects and rework. Vinyl wastes cannot be recycled in Tasmania.
Outcomes
What was implemented?
- A cloud-based App was introduced for recording waste in process.
- A dashboard and weekly Toolbox meeting provide real time feedback on performance for staff and the opportunity to learn from mistakes.
- Staff developed and implemented their own quality control process to reduce rework from errors in artwork.
Key issues
- How to improve the accuracy of reporting – developing appropriate tools to collect data.
- How to get people to use the error reporting tool – removing ‘blame’ from the process and raising the status of waste as a quality performance indicator.
Performance against targets
- We are confident that staff are reporting 100% of the nonconformances detected. However, this means…
- Our rework levels appear higher! But, now that we have an accurate picture of the problems, we can focus on target areas for reducing rework.
Lessons Learnt
- You can’t do it overnight, it takes time and effort to address cultural issues.
- As businesses, we need to lead the way and help our customers make good choices.
- Once staff are onboard, it becomes easy.
- This is a continuous process for us – there is no end date.
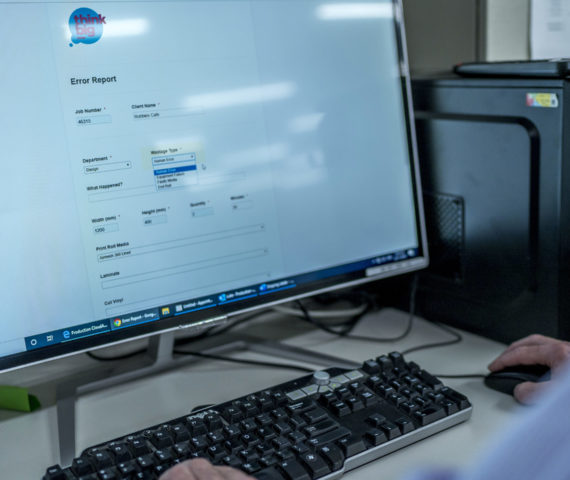
A device enabled App allows anyone to report errors and provides transparency. In response, staff developed their own quality control system to prevent errors in artwork proceeding to production.
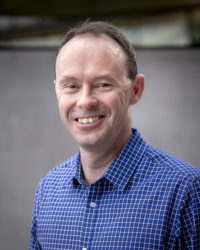
Scott Lovell
Owner/Manager