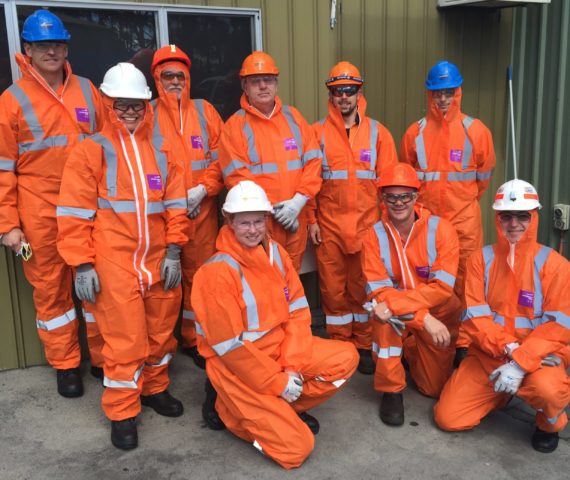
Lean Leadership
Program Objectives
- To further develop potential leaders identified through participation in previous Lean Action Learning programs
- Determining, implementing and managing competitive systems and practices across an organisation
- To spread lessons learnt from earlier Lean Action Learning programs deeper into each of the participating companies
- Qualification in a Diploma of Competitive Systems and Practices (MSS50316)
Key measurables
Each project provides a vehicle to apply Lean Leadership skills in a practical setting. Particular care is taken to identify specific, measurable outcomes for the implementation. Typically these will include targets for reduced lead time, improved on-time delivery, improved quality, safety and job satisfaction and ultimately improved profitability, as measured against a balanced scorecard.
Participants will be required to be proactive in determining the units appropriate to their learning needs and developing their own learning plan, in alignment with the measurable targets, and with the guidance of the mentor/facilitator. This plan will be discussed and agreed to with the participant’s manager.
Who should be involved?
Participants are likely to be in a managerial role, or to have potential for a managerial role.
Determining, implementing and managing the implementation of competitive systems and practices across the organisation, or a significant section of the organisation must be an intrinsic part of their job role.
Certificate IV in Competitive Systems and Practices (MSS40316) is a prerequisite to commencing the Diploma of Competitive Systems and Practices. There may also be prerequisites for specific Units of Competency within the qualification however there are no other mandatory requirements for participants commencing the program.
The action learning process
A Lean Leadership program involves atleast three companies, each nominating one person to the program.
The basic format of the program is similar to the Lean Action Learning program, ie.:
- Each company hosts a project
- Five workshop sessions per project
- Six to nine months implementation
Whereas regular Lean Action Learning projects tend to be specific to a particular process or system these will be higher-level strategic projects involving a comprehensive improvement plan for each company. Each plan will involve a series of projects and other initiatives to be led by the Lean Leader internally within their company.
The team is self-directing with remote mentoring and assessment by a suitably qualified action learning facilitator.
Participants work together as a team to develop their project plans, each person is involved in three projects.
Each individual is then responsible for leading implementation of their plan in their company, as an internal change agent.
The team will meet regularly as a cohort to review progress and will present the outcomes of the project to the BALT community at a combined review forum.
Want more information? Try our FAQs or email learn@actionlearning.edu.au