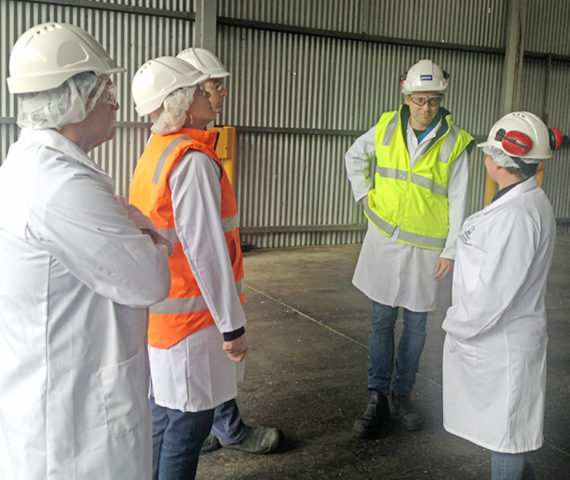
Tasmanian Alkaloids Seed cleaning process project
Project Objectives
- Increase yield of poppy seeds
- Streamline the poppy seed cleaning process
- Increase recovery rate to established target for next year
- Stay within the HACCP certification requirements
- Present recommendations for improvement
Project Team
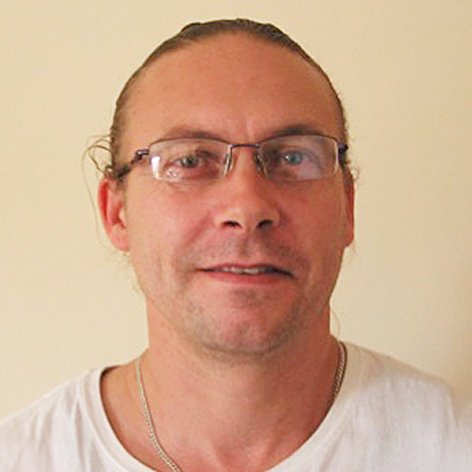
Peter Wilkins
Tasmanian Alkaloids
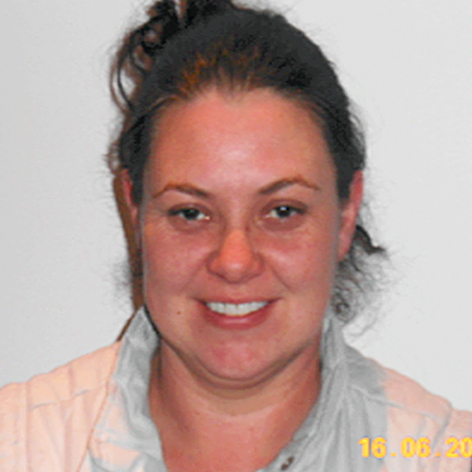
Natalie Page
Tasmanian Alkaloids
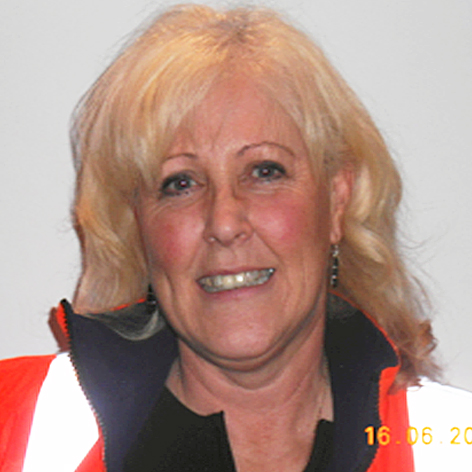
Robyn Lapthorne
TasRail
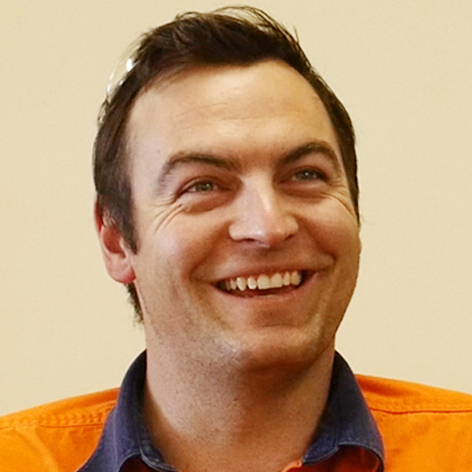
Brendan Sherriff
Bell Bay Aluminium
Facilitators
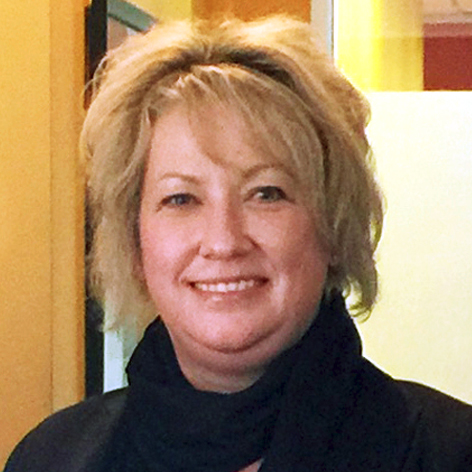
Roxanne Chugg
Excellent Outcomes
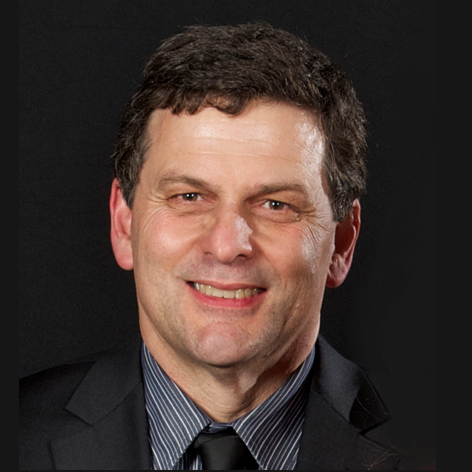
Bill Woodworth
Bell Bay Aluminium
Key measurables
- Poppy Seed yield per annum
- HACCP audit results
Companies involved
- Tasmanian Alkaloids
- TasRail
- Bell Bay Aluminium
Approach taken
- Detailed briefing from senior management
- Reviewed current seed cleaning processes
- Detailed process walk-arounds to identify waste (WORMPIT) and understand each aspect of the current process
- Created a ‘current state’ value stream map
- Try-storming to establish settings on Cimbria and Gravity tables to identify the bottle-necks
- Developed a storyboard to highlight potential bottle-necks, causes and process improvements
- Used the SMED process as part of the recommendations for improvement
- Stakeholder input – spoke to all shifts across the seed cleaning area
- Produced costing model to set financial targets
- Established implementation plans for key improvement initiatives
Summary of outcomes
- Updated procedures and work instructions completed with a trouble shooting guide
- Quick change over procedure established for line clearance for cleaning plant
- Waste streams are now generating revenue not cost
- Machinery modified for better access for cleaning and maintenance
- KPI’s put in place to track progress
- Throughput increased by over 50%